LeanCompany™ is a consulting process that identifies and eliminates waste, especially in overlooked areas behind the scenes, both in the field and in internal operations, revealing significant cost savings.
This process gathers insights from every employee on the front lines and in the back office, including those responsible for handling paperwork, estimating jobs, selling homes, and managing projects. This process does not cut essential business services, reduce critical staff, or harm the customer experience. Instead, it focuses on removing waste in product, process, and procedures that do not add value for customers, both internal and external
LeanCompany can be implemented for organizations of all sizes and is ideal for previous participants of a LeanBuilding Blitz™.
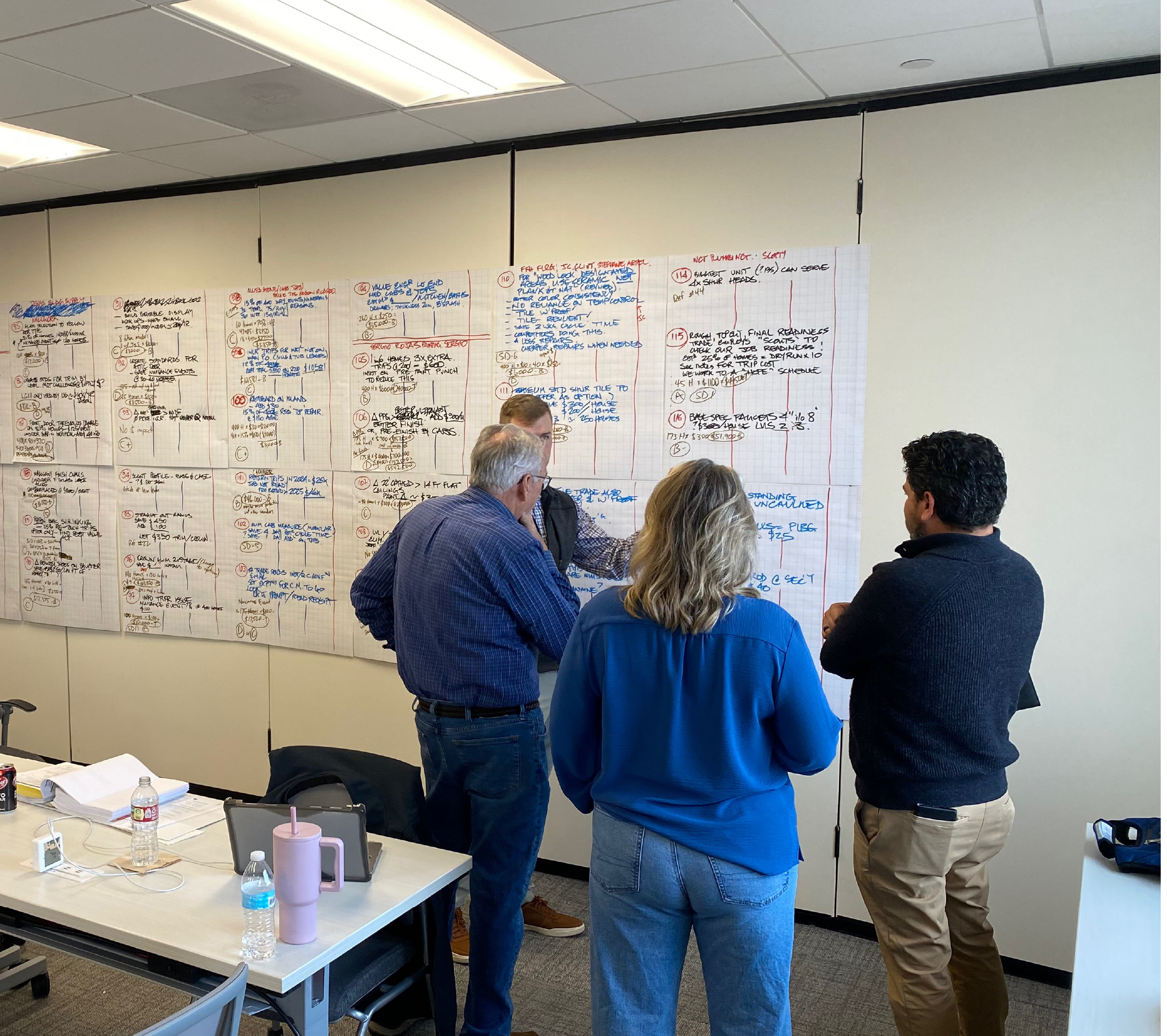
PARTICIPANT SELECTION
The LeanCompany workshop approach harnesses the knowledge and insights of all employees, ensuring that each team member contributes to the improvement process. Ideally, the multiple department teams should consist of 8 or fewer participants to maintain accountability. However, involving everyone in the organization in a team can significantly enhance idea generation and foster enthusiasm for implementation.
Typical teams may include:
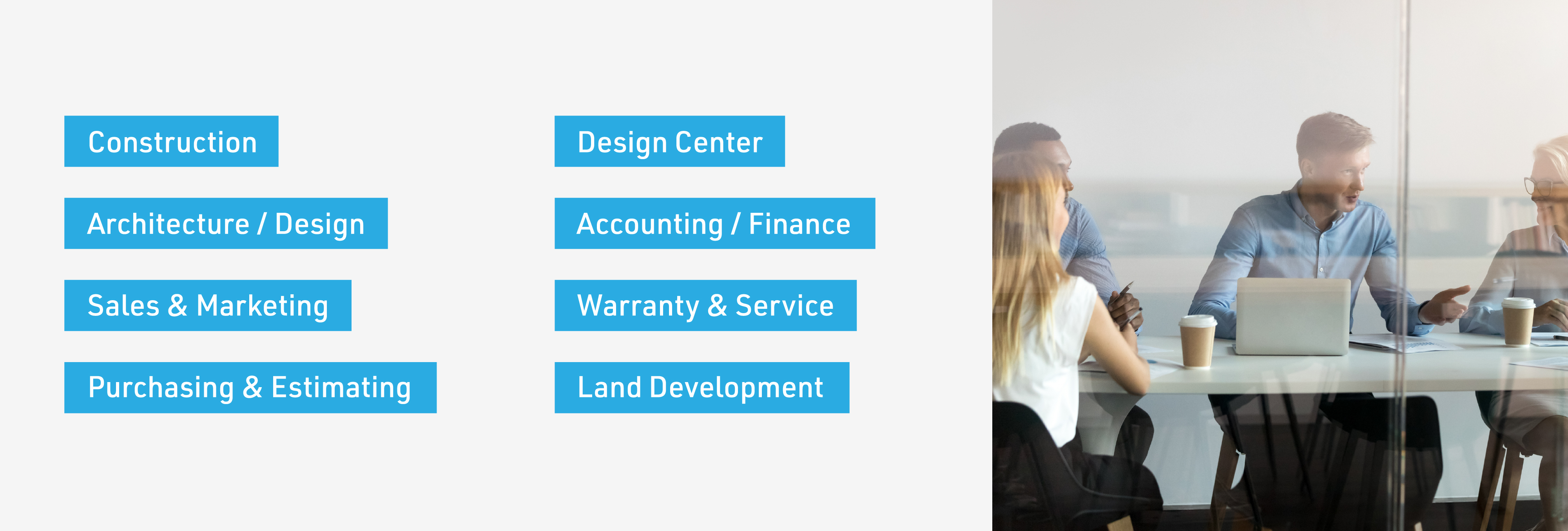
PROCESS
This LeanCompany process provides a structured approach to achieve the cost-saving results your company seeks. It identifies the cost-cutting opportunities you need— without cutting corners or damaging relationships– and serves as a highly effective team-building process.
One Day
TrueNorth Consulting conducts an in-person Lean Process orientation for the entire LeanCompany employee team – at all functions and levels. This session provides an overview of Lean principles, emphasizing their application in homebuilding and within your company.
By following the LeanCompany process, employees will learn to identify waste in their work, departments, and interactions with other teams, suppliers, and trades. Insights from our LeanBuilding Blitz implementation are also shared.
By the end of the session, each employee departmental team will generate multiple improvement ideas that require further investigation and analysis.
Two to Three Weeks
After the orientation, each department independently develops and refines its improvement ideas following the initial orientation and idea generation day led by TrueNorth consultants.
These consultants will return in two to three weeks, giving the department groups time to analyze and prepare their suggestions thoroughly. Representatives from each department will organize their waste reduction ideas and prepare them for presenting to the Builder Lean Team in a specified format.
Two to Three Days
TrueNorth’s Consultants explain the process for the upcoming days and prepares the Builder LeanTeam with essential listening skills. During this time, representatives from each department present their ideas to the experienced Builder LeanTeam, established during the LeanBuilding Blitz workshop. The LeanTeam members ask clarifying questions to ensure they fully understand the issues while maintaining a non-judgmental approach.
This process is nearly identical to the supplier/trade presentations to the Builder LeanTeam, with departmental teams taking the same role of suppliers and trades.
One Day
The Builder LeanTeam collaborates with Senior Management to evaluate ideas based on their value and difficulty, selecting the most promising ones for further development.
These ideas are prioritized using the LeanBuilding Blitz ABCD Matrix, and champions are appointed to lead their implementation. Action plans are created for the top 10-12 ideas to guarantee early success.