“Lean,” as in “Lean Thinking,” “Lean Methods,” or “Lean Operations,” is not a term for running a bare-bones operation. Lean methods have revolutionized companies and industries worldwide, yet the homebuilding industry has largely overlooked Lean practices— until now.
Lean is a flexible model not limited to any specific industry and is used to improve quality and efficiency. Industries ranging from automotive to electronics, healthcare, and insurance have undergone significant transformations by implementing Lean practices.
The construction industry has seen little change in productivity for over a century. Statistics show almost no productivity improvement for homebuilding over the past 50 years, the single worst record of all American industries. A lack of collaboration and innovation among builders, suppliers, trades, and manufacturers has resulted in inefficient building methods and tremendous waste. Labor shortages, inefficient supply chains, and rising costs compound the situation. As margins are squeezed, the need for builders to identify savings opportunities increases. The TrueNorth™ Consulting difference means cost savings are achieved for all parties involved.
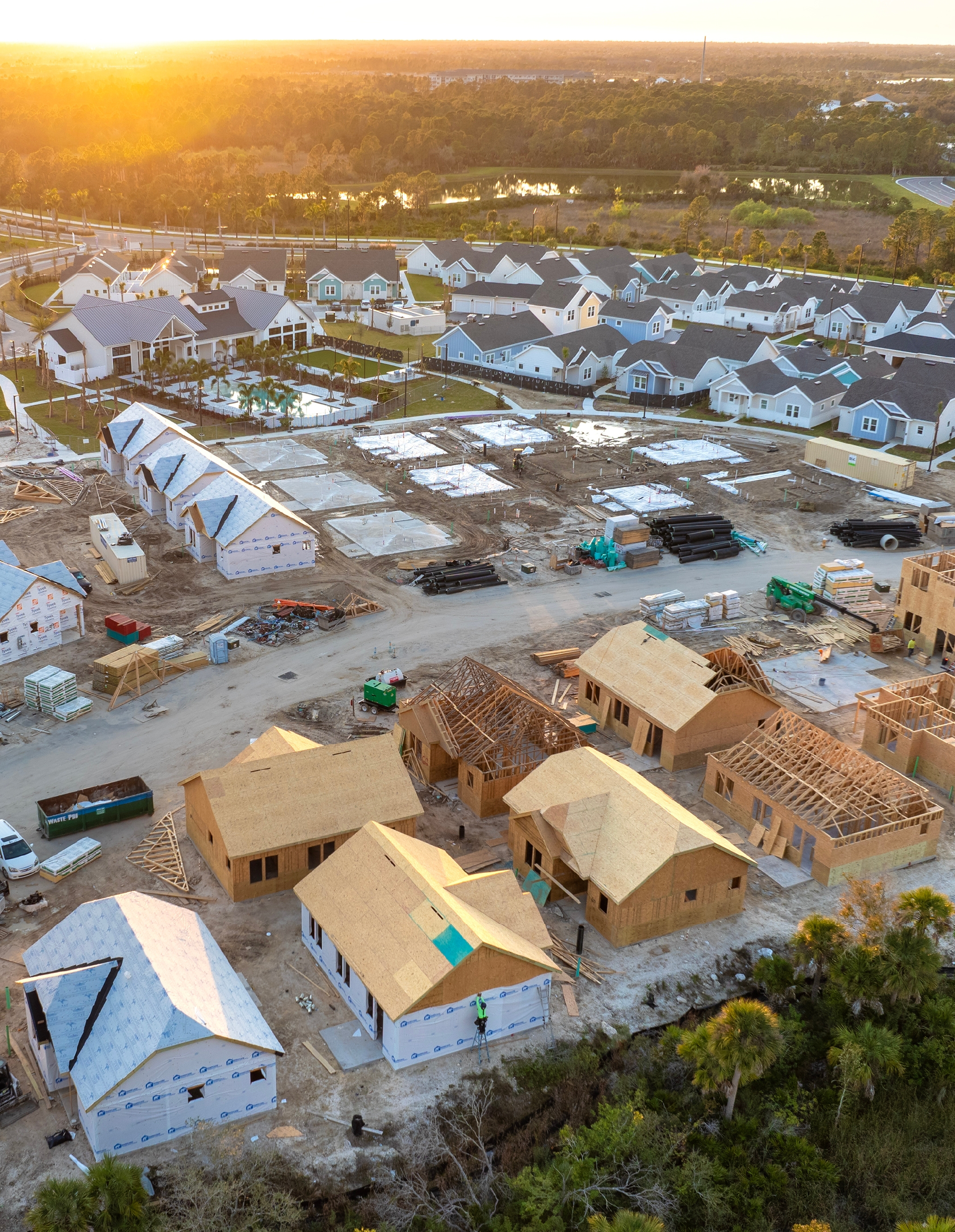
New opportunities
Traditional cost-cutting methods often compromise operations and fail to improve profitability. MiTek® TrueNorth™ Consulting combines extensive homebuilding knowledge and Lean practices to deliver a tailored experience, helping you stay competitive in an evolving market.
Traditional Methods
- Slash overhead, often making it more challenging to conduct business
- Cut headcount, making it difficult to staff builds
- Force supplier rebids, straining those relationships
- Reduce house features, making them harder to sell
- Use traditional stick framing
Lean Homebuilding Methods
- Eliminate non-value-added steps, materials, and procedures
- Shrink work-in-process and cycle time
- Improve processes with permanent solutions instead of temporary fixes
- Deliver high-quality homes on time, with less inventory in the system
- Incorporate component design whenever possible to reduce errors, rework, trips to the job sites, and shorten cycle time